Several commonly used mechanical repair techniques
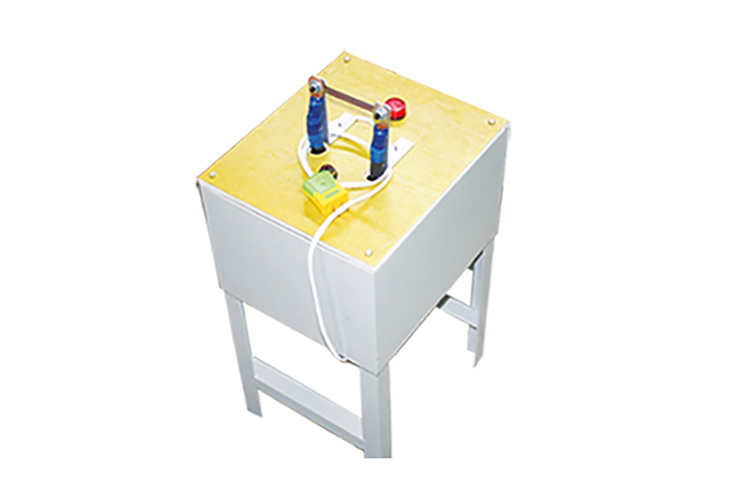
(1) Welding. Including: surfacing (which can repair the wear of non-matching parts and parts that can be processed to the original shape after surfacing), spot welding (which can eliminate connection fasteners, local scratches, and repair welding), repair welding (Compensation for wear) Plasma welding, spontaneous combustion welding (suitable for field operations).
(2) Brush plating, also known as slotless plating. This is a mature technology that has been applied for 30 years. It can repair the local wear of parts with simple facilities, especially the local wear of large parts. In recent years, brush plating technology has made new progress. For example, nano brush plating technology can greatly improve the mechanical properties of the coating.
(3) Spraying technology. It can not only compensate for the wear of the parts and restore the geometric dimensions, but also improve the surface properties of the parts. For example, spraying special materials on different base materials to achieve anti-corrosion and wear-resistant effects. Now, spraying technology is developing rapidly. In February 2004, the research project of the National Defense Science and Technology Key Laboratory of Equipment Remanufacturing Technology of the Academy of Armored Forces Engineering, "Research and Application of High-Performance Supersonic Plasma Spraying Technology", won the second prize of the 2005 National Technical Invention Award and the second prize of the National Science and Technology Progress Award . In addition, cold spraying has appeared in recent years (thermal spraying has its drawbacks: the spraying material is oxidized).
(4) Adhesive coating technology. A composite material composed of high molecular polymers or inorganic compounds and special fillers is coated on the surface of the worn parts, and after curing, the mechanical processing can be carried out to restore the size and accuracy of the parts and achieve the original performance. This method is especially suitable for the repair of large parts. For example, Xuzhou Construction Machinery Group Company applied adhesive coating technology (resin plus curing agent, processing after 24 hours) to eliminate large-area wear on the inner wall of a 500t press cylinder (φ500mm×1300mm), causing serious failures of oil drainage and pressure reduction between the cylinders and pistons. The repair cost is only 1/20 of the replacement cost.
(5) Bonding technology. Bonding technology includes bonding materials and bonding processes. At present, bonding materials have formed a family, which is divided into several series according to different bonding materials and uses. Each series is divided into different specifications, and the application is very wide. Typical is Germany, there are more than 900 kinds. The bonding strength is not lower than the strength of the base material. For example, on the A380 aircraft, one-third of the parts are glued out. In addition, patch technology (industrial band-aids, used to repair leaks in pipelines) has emerged in the industry.